近年來隨著國家環保督察力度的趨嚴以及專用車行業降本增效的大勢所趨,專用汽車行業產線升級正如火如荼。
除了在下料、切割和焊接等工藝的提升外,專用車領域一種新的涂裝工藝——噴粉工藝,自2016年使用后,這項全新的涂裝工藝已經得到行業的廣泛認可,并且引發示范效應。
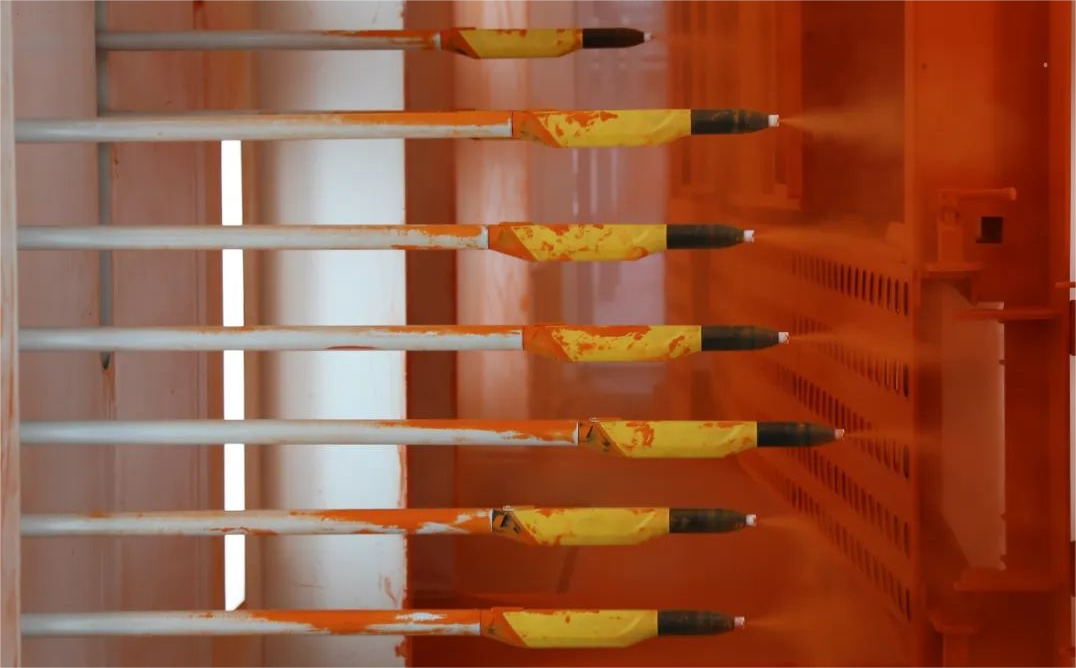
以半掛車為例,山東蒙陰、山東梁山、河南駐馬店等均建成全新的噴粉線。
不同于使用水性漆的傳統溶劑型工藝,噴粉工藝是如何誕生的?與傳統溶劑型工藝有什么不同?我們今天來聊聊。
噴粉工藝的歷史最早可以追溯到上世紀四十年代,采用火焰噴涂法將粉末涂料涂敷于金屬底材上,但進度緩慢。
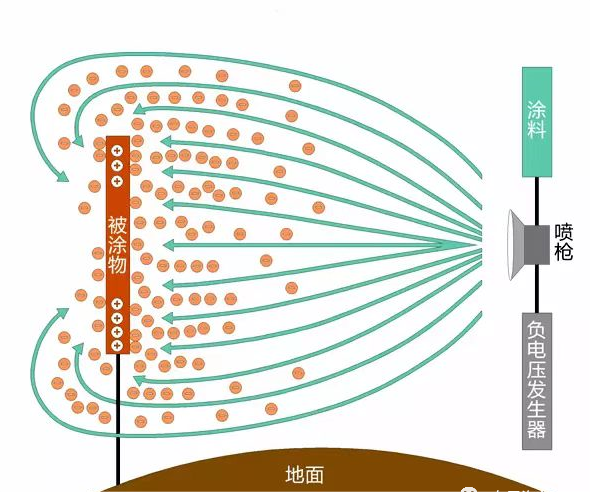
1954年德國的詹姆將聚乙烯用流化床法涂覆成功,1962年法國的塞姆斯公司發明粉靜電噴涂后,粉末涂裝才開始在生產上正式采用。
噴粉工藝得到進一步發展源于粉末噴槍的誕生。1967年,瑞士金馬公司研發出世界第一把靜電粉末噴槍。
當時,高壓發生器為外置式,體型比較龐大,操作性和靈活性也相對較差。1973年,瑞士金馬公司革命性地將高壓靜電發生器集成到了噴槍的內部。這一突破性的研發,成為了靜電粉末噴涂設備發展歷史上重要的里程碑,沿用至今。
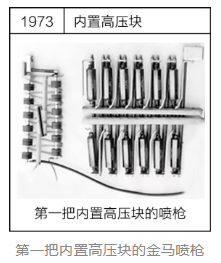
我國的噴粉工藝研究開始于上世紀六十年代,幾乎與國外同步。最初應用在防護和電氣緣方面,隨著科技的發展,噴粉工藝已廣泛使用于電氣絕緣、耐腐蝕化學泵、閥門、汽缸、管道、屋外鋼制構件、鋼制家具、鑄件等表面的涂裝。
中集車輛的示范引領
20世紀70年代初,粉末涂料初步應用于汽車領域。由于汽車涂料有高耐候、高耐腐蝕、高耐磨,以及耐熱、保光保色等性能要求,技術進展相對緩慢。
粉末涂料初期應用僅局限于汽車零部件、汽車底涂等,后來逐步用于汽車底面合一粉末涂料和粉末罩光清漆,成為真正意義上的汽車用粉末涂料。20世紀80年代,日本的Honda、意大利Fiat開始使用粉末涂料噴涂汽車車身。
我國粉末涂料在汽車工業中的應用大多在汽車零部件方面,雖然以其優異的涂層性能和環保性能已經完全可以替代液體涂料,但受產品結構和涂裝技術限制,我國粉末涂料占汽車涂料應用市場不到10%,而歐美國家適用于汽車零部件噴涂的粉末產品已經達到50%以上。
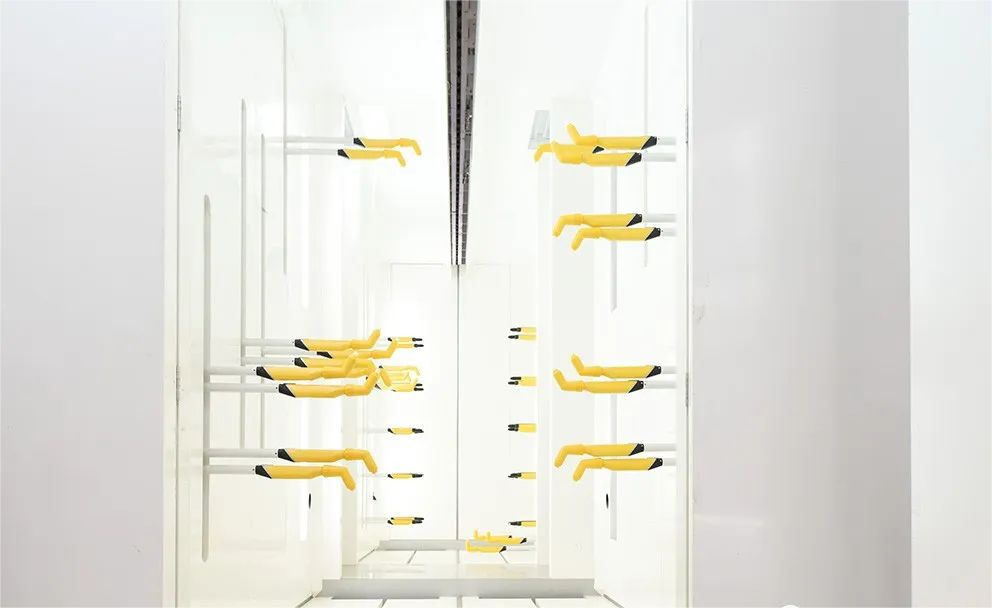
2014年1月,以探索數字化工廠樣本為目標的“燈塔工廠”在東莞中集正式啟動,隨著中集車輛“燈塔工廠“建設的不斷深入,由此也讓噴粉工藝進入行業視野。
中集車輛的”燈塔工廠“為示范引領,噴粉工藝在環保督察日漸加嚴的大背景下,很快憑借經濟性和環保性的特性得到專用車企業的青睞。
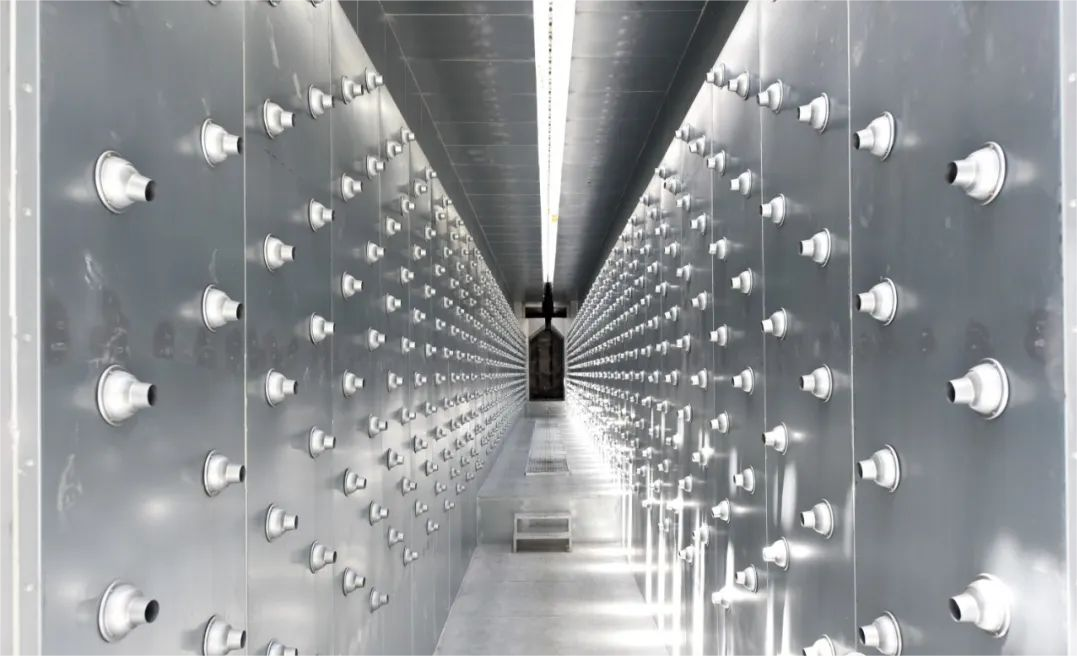
相比于油性漆,噴粉工藝的VOC排放為零,對油漆的利用率可從40%提高到90%;而相對于水性漆,又可降低40% 以上的制造成本,而且產品的涂裝品質成倍提高,保修期限可由現在的5-7 年提高到10年之久。
噴粉工藝的日漸成熟
噴粉工藝最早應用在半掛車產品,特別是平欄倉等相對標準化的半掛車產品。
2018年,中集瑞江產線升級項目啟動,以攪拌車為核心進行工藝升級。在此次改造項目中,中集瑞江采用粉末涂料噴涂,選用底粉+面粉雙涂層的涂裝工藝,實現罐車涂裝線技術的全新突破。
噴粉線
此后,中聯重科、三一重工等頭部專用車企業迅速跟進,從而帶動罐式類專用車特別是攪拌車噴涂工藝邁入全新階段。
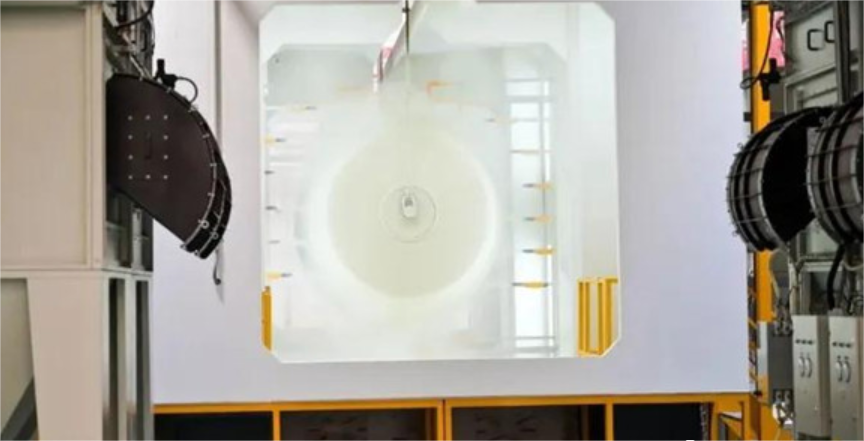
施維英噴粉線
2022年,山東專用車智能制造基地產品對噴粉工藝又進一步做了優化,率先在廂式專用車領域開展試點,在國內推出全國第一臺9.8米整體噴粉廂式廂。
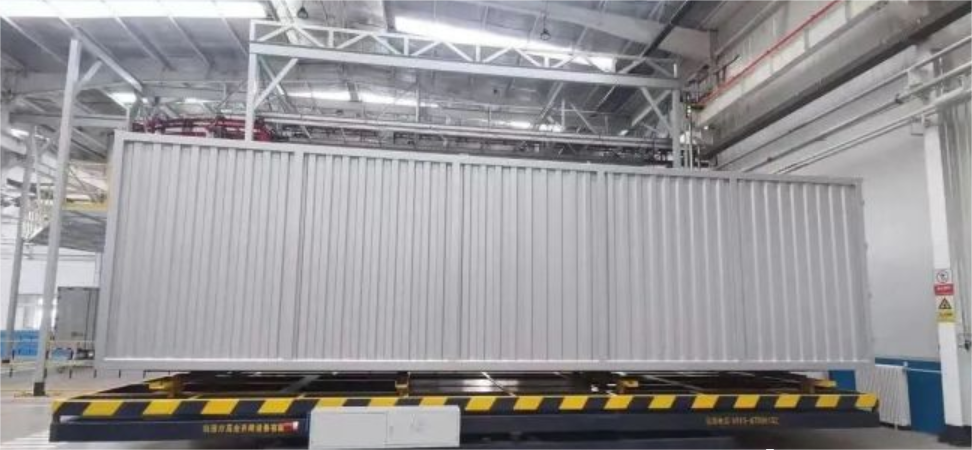
噴粉線
專用車智能制造基地配備的粉末噴涂系統,不僅是全國專用車行業最大的噴粉設備之一,能夠噴涂自卸車、廂式車、倉欄車多種產品,而且采用廂體粉末面涂工藝新型工藝,戶外銀色金屬粉末的大面積應用更是國內少有。
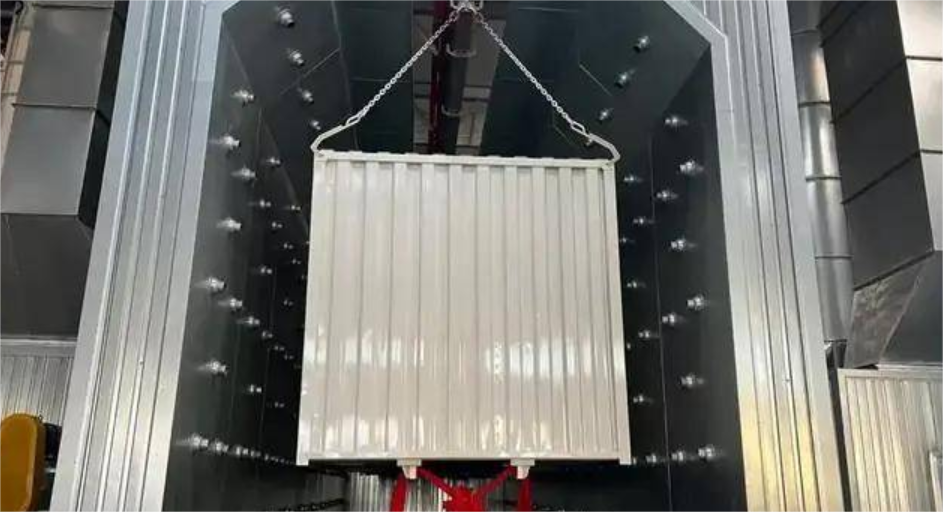
噴粉線
除了頭部企業的示范引領之外,噴粉工藝目前在半掛車、工程車、罐式車、廂式車、自卸車領域技術已經日漸成熟,并且形成了完善的產品方案。
以半掛車為例,甚至已經形成了兩條技術路徑:電泳底漆+粉末面漆雙涂層噴粉工藝和半掛車拋丸后采用前處理+底粉面粉或者底面合一噴粉工藝。
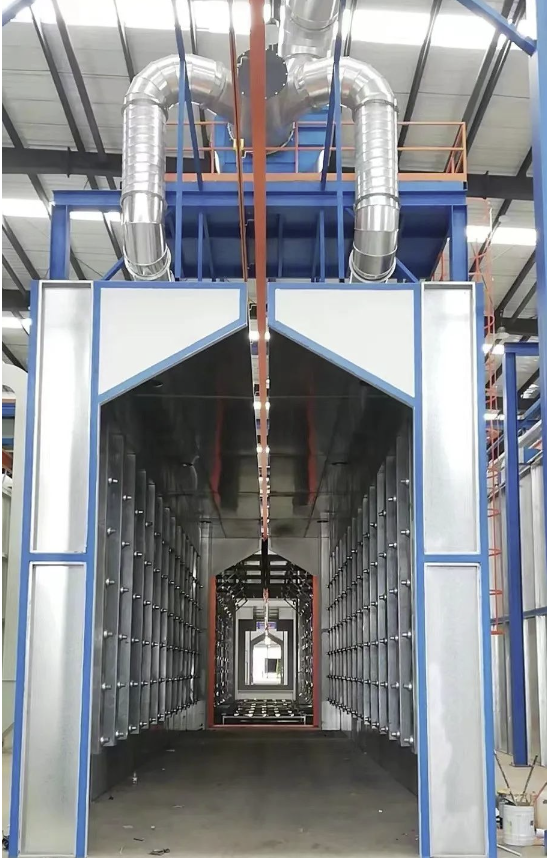
噴粉工藝的不斷迭代進步,一方面推動很多新建專用車企業、跳過“水性漆”階段,從油性漆直接改到噴粉工藝,如正在建設中的凱利重工就采用了瓊花涂裝的全套噴粉工藝,另一方面也促進了傳統涂裝企業的快速轉型,快速建設期的專用車噴粉項目也讓瓊花涂裝等一批專注專用車涂裝的企業實現從局部涂裝線改造到全套產品涂裝工藝的經驗積累。
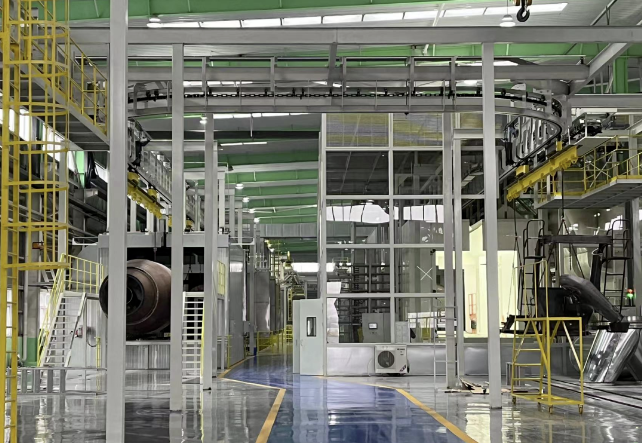
回顧專用汽車噴粉工藝發展史,從上世紀六十年代到現在,噴粉工藝歷經六十載才走進專用車行業。但,迎接噴粉工藝的機遇與挑戰,卻才剛剛開始。
套用狄更斯在《雙城記》中的一句話:“這是最好的時代,也是最壞的時代。這是希望之春,這是失望之冬;人們面前有著各樣事物,人們面前一無所有。”或許最為恰當了。